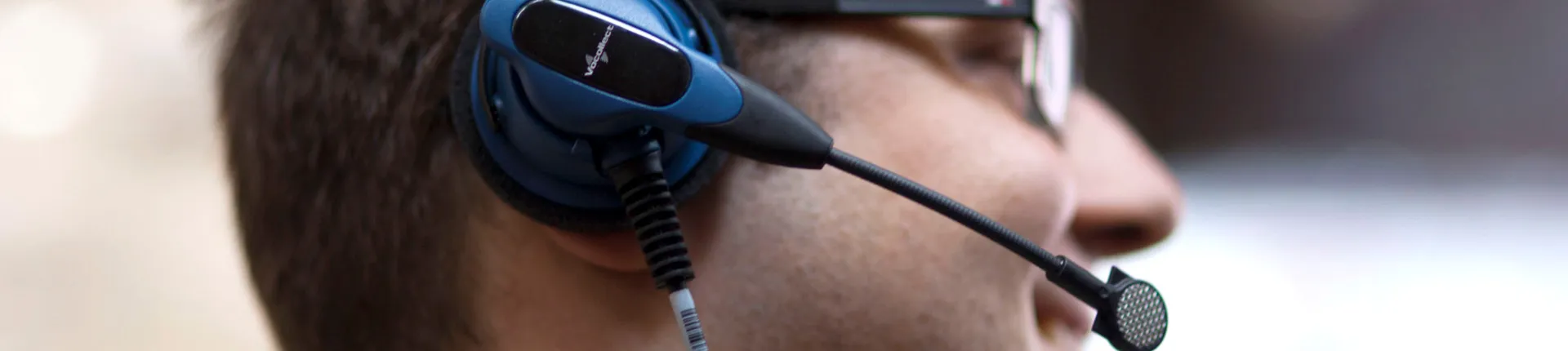
The ICU is able to deploy up to 4 new employees per week thanks to voice
The largest Czech food distributor JIP Východočeská is using voice technology to increase the productivity of warehouse operations and simplify the training of new warehouse workers.
About the customer
JIP Východočeská is a family-owned company, founded in 1994, focused on wholesale and retail food sales with nationwide coverage. JIS offers its customers a full range of products (colonial goods, beverages, non-food, drugstore goods, frozen and fresh goods), logistics and all services related to the modern sales process.
The JIS Group supplies its customers from 15 wholesale warehouses and plans to build new logistics centres in Zlín and Ostrava in the near future. The wholesale warehouses operate in a controlled warehouse management mode (FIFO system).
SITUATION BEFORE THE INTRODUCTION OF THE VOICE SOLUTION
Mutual cooperation in the supply of mobile terminals has been going on for several years. Thanks to the situation on the labour market, the Czech Republic has become a country with extremely low unemployment within a few years. The resulting shortage of qualified staff also affected JIP, which struggled to find employees for its central warehouse in Bořanovice, north of Prague.
Many of the 60 warehouse workers working three shifts at this warehouse come from Romania, Ukraine and other southern European countries. Many of them return home after having used up their three-month work permits.
"We meet four to five new warehousemen a week, usually none of whom speak Czech," says operations director Ing. Aleš Groulík. The JIP was therefore looking for a solution that can simplify the training process and enable flawless performance in the shortest possible time. In addition, it was necessary to make the dispensing process much more productive in order to effectively counter the annual sales growth (10%) without having to hire new staff.
PROJECT OBJECTIVES
- Increase productivity and efficiency of warehouse operations
- Train new employees as efficiently as possible
- Simplify and more quickly onboard new employees
- Reduce the cost of repairs to counters and mobile terminals
- Improved working conditions and employee satisfaction
- Increased transparency of warehouse processes
SOLUTION
Based on these facts, we proposed to use and implement Honeywell Voice technology. Within 4 months of deployment, the first users working with voice technology had already stopped working with manual scanners.
The warehouse worker communicates with the system using speech, so they don't have to waste time reading commands from the terminal display or confirming them with the keyboard. Orders are first transmitted from the WMS to the K.voice module, which sends them via WLAN to the Talkman voice device. Talkmen then generates the voice commands and sends them via Bluetooth to the operator's headset.
New employees learn these steps in the workflow very quickly because the system is multilingual. Warehouse workers can therefore start working immediately, leading to easier training and thus faster achievement of expected productivity.
The K.voice system solution provides management of all devices - terminal status, battery life and it is even possible to influence the functionality of the system and easily deploy new versions of voice dialogues.
RESULT THROUGH THE EYES OF THE CUSTOMER
"KODYS, spol. s. r. o. is our long-standing supplier of terminals and readers. They were the winner of the tender thanks to their own K.voice solution for voice technology. During this period, KODYS has grown from a hardware supplier to a system and consulting company", says Aleš Groulík.
"The training of new employees works very well because the system is multi-lingual. Due to the situation on the labour market, we have not avoided using foreign workers. It is very comfortable for them to be trained in their native language and according to the experience we have with the system, we can have a worker fully prepared within three days of training, and there is a high turnover of employees. This means that we are training 4 to 5 people a week and we don't have the slightest problem with that," he added.
"We can see what each warehouse worker actually does, for example how fast they work and how much time elapses between two orders. With voice picking, we've been able to increase productivity by 20% while reducing the cost of repairing faulty readers and terminals, which has a significant impact on the cost of this branch."
Ing. Aleš Groulík
Chief Operating Officer of the ICU Východočeská, a. s.