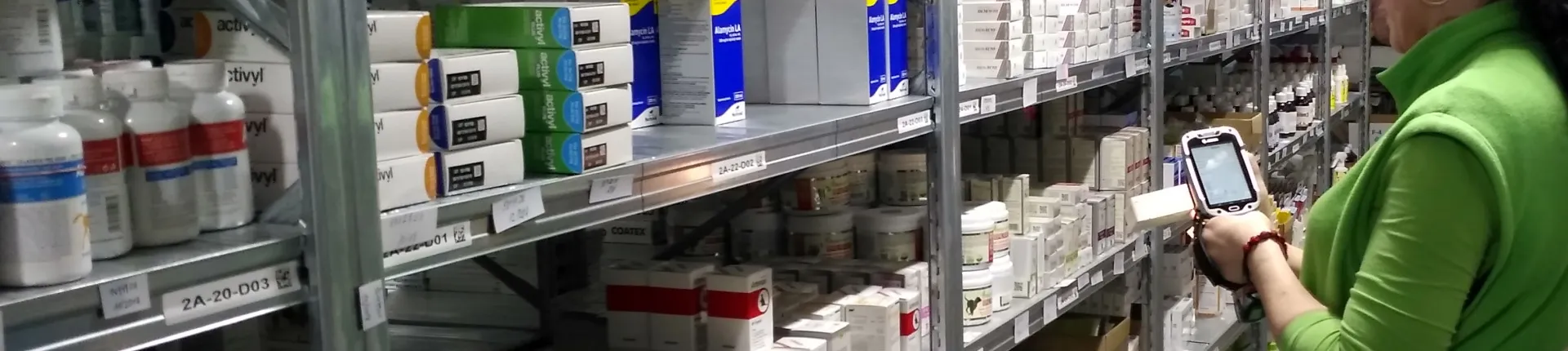
WMS system reduced the error rate and streamlined warehouse processes at PHARMACOPOLA
PHARMACOPOLA is a Slovak distribution company with more than 10 000 items in stock. It has been on the market for 25 years and since the beginning it has focused on wholesale distribution of veterinary medicines and preparations. Since 2001, its portfolio has expanded to include the sale and distribution of feeds, and later it established an instrument division. Today, PHARMACOPOLA is the exclusive partner of several global manufacturers of veterinary products, feeds, breeding supplies and instruments.
Original condition:
PHARMACOPOLA's warehouse, with an area of more than 2,500m2, is divided into 3 logical units - feed, veterinary pharmaceuticals and human pharmaceuticals. In each of these warehouses, goods of different nature are handled, which increased the demands on the functioning of the warehouse as a whole. Another specificity was the tracking of batches and expirations for goods. The nature of the goods stored also adds to the complexity, as veterinarians require delivery of the ordered medicine no later than the next working day after ordering.
The warehouse was managed in the Navision ERP system using pen and paper, meaning that warehouse staff were given paper documents against which they made receipts and dispatches and in which they recorded the movements of goods in the warehouse. In order to achieve a low error rate, it was necessary to perform additional tasks for each operation, which slowed down the individual processes and increased the administrative burden on the warehouse operation. To facilitate the traceability of goods in the warehouse, goods were stored in precise positions, which limited the efficient use of warehouse space. If goods were moved within the warehouse, it was administratively difficult to change them. "When we needed to move goods within the warehouse to a different position, the warehouseman would note the change on paper and later, when he got to the computer, he would note the change in the information system, causing us to have outdated information in the system about the location of the goods".
Milan Greguš,
Director of Logistics at PHARMACOPOLA
Introduction of the WMS system
The original way of working was not efficient enough and with the increasing number of orders, PHARMACOPOLA had to consider introducing a WMS system that would best meet its needs and enable it to meet the ever-increasing demands of its customers in order to maintain its leading position in the market.
Main objectives
- streamlining warehouse processes
- reducing the error rate in warehouse operations
Secondary objectives
- real-time overview of stock and stock location by position
- optimisation of human resources, reduction of employee turnover
- obtaining indicators for evaluating the work of warehousemen
With the introduction of the HighJump Warehouse Edge WMS (formerly AccellosOne Warehouse), these objectives have been achieved. Warehouse workers work with mobile terminals, with barcode scanners, which they use to carry out individual operations such as receiving, picking, moving and inventorying goods. As a result, individual operations are carried out more quickly and easily, while keeping error rates to a minimum.
All movements are recorded online in the system, so that all warehouse staff, as well as staff in other departments such as purchasing or sales, have up-to-date and accurate information on the status of goods in stock at all times. Of course, batches and expirations are tracked for individual operations.
For faster and more efficient order picking, warehouse staff can use the wave picking function, which allows them to pick goods for several orders at once in one pass through the warehouse.
Another benefit is that the system provides detailed information about the work of individual warehouse workers. "Thanks to the WMS system, we now have accurate information on the performance of individual warehouse staff, so we can reward people fairly according to their actual performance."
Milan Greguš,
Director of Logistics at PHARMACOPOLA
PHARMACOPOLA's warehouse operates in a three-shift operation 6 days a week, so the system's start-up had to be fast and smooth. Thanks to the cooperation of all parties involved, this was achieved and the system was in full operation the very day it went live. Half a year after going live, a total of 26 warehousemen are using HighJump Warehouse Edge in the warehouse without any major outages. On an average day, the system processes around 500 orders and is ready to scale up further. It can be stated that thanks to the introduction of the system, a streamlining of warehouse processes has been achieved, thanks to which the warehouse is able to handle a larger number of orders without the need to increase the number of staff in the warehouse.